There are numerous factors which contribute to the low productivity of animal production countries. One major constraint is the high population density and the competition of human and livestock for feed resources. Also there is a one sided development most developing countries have significantly improved their breeds and numbers of livestock.
There has however been no real increase in animal or human feed production and no economically viable feed substitutes have been developed. Under nutrition is still the major limitation to increasing livestock production in these countries. Because of the high cost of feed ingredients, the available feeds are usually low in metabolizable energy and protein. In some instances and even with apparently adequate feed supply animals have been observed to deteriorate.
This may be attributed to at times poor quality feed ingredients and a wide variability in nutrient composition often leading to subclinical nutrient imbalances, deficiencies inessential nutrients and/or toxicities associated with mycotoxins or salmonella leading to ill-thrift. This problem of low metabolizable energy and protein leads to the legislation and quality control for commercial feed formulation.
Legislation on Animal Feed
Legislation on animal feed is harmonized at European Union (EU) level. It applies principally to feed for farmed livestock, but also covers feed for horses, pets, farmed fish, zoo and circus animals, and creatures living freely in the wild.
Labelling and Composition
Legislation on the labelling and composition of animal feed covers:
- The information to be provided to purchasers on feed labels.
- The nutritional claims that can be made for certain feed products
- The names and descriptions to be applied to various feed materials (that is, ingredients either fed singly or included in compound (manufactured) feeds).
- The additives (including vitamins, colourants, flavourings, binders) authorised for use in animal feed.
- The maximum levels of various contaminants (e.g. arsenic, lead, dioxins and certainpesticides).
- Certain substances that must not be used in feed.
Quality Control in Feed Formulation
Quality control in feed production is of utmost importance in the overall success and profitability of animal enterprises. There is no other factor, directly or indirectly related to the proper nutrition and high performance of animals that is more critical than feed quality control and ration consistency.
The degree of quality is the consistency in which feed is formulated, processed, mixed and delivered as compared to what is expected. Animals thrive on a routine and respond better if the feed is low in nutrient variation as offered to them; and is similar in moisture content, texture and rate of energy availability.
Quality has been defined as any of the features that make something what it is and the degree of excellence which a thing possesses. Either definition may be acceptable if one recognizes that quality control means knowing the quantitative amounts of all components, good and bad, in a feed. However, relative values of quality over time are extremely valuable and useful in many situations.
The relationship between feed quality and animal performance is important and encompasses not only the quantitative amounts of all feed components, but also the digestibility and metabolism of those components.
Thus, the challenge for nutritionists and others involved in animal feed production is to consistently monitor all aspects of the feed production system used and measure those variables that are good indicators of quality control.
For the feed industry, a quality control system is the responsibility of management and involves properly trained personnel to ensure a high level of organization, documentation, and the policing of various procedures and processes necessary to guarantee the basic quality of feedstuffs and feeds.
Read Also : Feed Manufacturing Process and Methods
Determining Quality of Incoming Ingredients and Outgoing Feeds
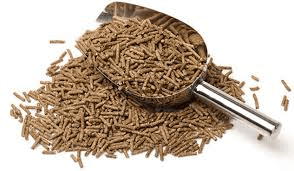
Quality control of incoming ingredients is crucial to predicting the quality of a complete feed, supplement, premix, etc. An. important first step is accurate sampling and complete examination of the ingredient prior to unloading.
Put sampling and inspection procedures in writing and keep them in a quality control procedures manual. The goal in sampling any lot of ingredients or finished feed is to obtain samples that are representative of the lot in question.
A wrong answer which may arise from incorrect sampling, incorrect handling of samples, analytical error, etc. is worse than no answer. Thus, it is our responsibility to know proper procedures and techniques for sampling to be sure that correct formulations can be made. Below are some suggested sampling procedures for bulk ingredients and mixed feeds, bagged ingredients and mixed feeds, hays, and syrups and fats.
Read Also: Effect of Feeding Fresh Cassava and its Peels to Ruminant Animals
Bulk Ingredients and Mixed Feed
- Take a minimum of three, 2.25kg samples.Each sample should be the composite of several cores taken randomly from the delivery truck, bulk storage bin or feed bunk, as applicable.
- Duplicate determinations are recommended for all variables measured samples
- Each sample should be the composite of several cores taken randomly from the delivery truck, bulk storage bin or feed bunk, as applicable.
- Duplicate determinations are recommended for all variables measured.
Bagged Ingredients and Mixed Feeds
Use slotted feed trier for sampling and take 0.50kg samples.
For lots of one to ten bags, sample all bags.
For lots of eleven or more, sample ten bags.
Analyze a minimum of three samples and average the results.
Hays
For chopped hay, take ten samples per lot.
For cubes, take forty cubes from a given population.
For bales, take one twelve to eighteen inch core from the end of forty bales in a given population.
Syrups and Fats
Use a continuous flow sampling procedure at the point of delivery, or a core liquid sampler.
Establishment of a retention schedule is recommended for all ingredient and mixed feed samples. Separate analytical analyses should be routinely performed on samples of the following for quality:
- Water.
- Grains.
- Roughages.
- Silages.
- Protein supplements.
- Mineral mixtures.
- Vitamin premixes.
- Molasses and fat.
- Specific drugs.
As a starting point for insuring quality in feedlot rations, quality check all incoming feed ingredients for the following:
- Moisture
- Color
- Off odor
- Presence of foreign material
- Texture and uniformity
- Evidence of heating
- Deterioration due to biotoxins
More detailed analyses are performed on individual feed ingredients for the purpose of feed formulation, and sometimes before the purchasing of commodities if this information is not provided by the seller.
Analyses that usually are considered to be routine for the different feed ingredients include:
- Grains – grade, moisture, protein, ash
- Grain By-Products – moisture, protein, ash
- Dry Roughages – moisture, protein, ash, acid detergent fiber
- Silages – moisture, pH, temperature, protein, ash
- Protein Supplements – moisture, protein, ash, non-protein nitrogen
- Mineral Mixtures – moisture, specific nutrients
- Molasses – moisture, ash
- Fats – moisture, free fatty acids, impurities, unsaponifiables
Derive an overall evaluation of feed quality delivered by determining the variation in the four major areas that affect feed consistency. They are:
- Variation of incoming ingredients
- Variation in feed mixing efficiency
- Variation in efficiency of delivery of mixed feed from mixing point to the animals
- Variation in analytical procedures
Use of Current Good Manufacturing Practices in Maintaining Quality Control

The management of a feed mill has an obligation to uphold Current Good Manufacturing Practices (GMP).
The use and endorsement of appropriate and proper procedures and practices in the production of feeds do not cost the feed industry.
The feed mill manager is a key individual involved in the daily activities associated with the management of people, facilities and resources that ensure the procedures appropriate for the production of feed in the feed mill are enforced.
The feed mill manager, as well as supervisors and the people working under their direction, have an obligation to the animal food industry to maintain high quality standards in the production of feeds for animals to produce meat, milk, eggs, etc. for the consumer.
Good Manufacturing Practices were published by the Food and Drug Administration (FDA)in the November 30, 1976, Federal Register.
Good Manufacturing Practices deal specifically with the manufacturing of any feed containing one or more drugs. If any feed contains a drug, it is a medicated feed. The feed mill management should have written instructions that cover GMP’s and quality assurance programs.
Good Manufacturing Practices cover all areas involved in the production of feeds including personnel, facilities, feedstuffs, quality assurance checks, inventory control checks, processing methods, mixing procedures, finished feeds, and feed delivery.
Although commercial feed mills that produce and sell a complete line of feeds to the general public have a somewhat greater task in assuring quality and prevention of cross contamination of drugs, the obligation and importance in all feed mills are still great.
Outlines, checklists and procedures relevant to feed mill operations are presented below;
Conduct personnel training conducted periodically to assure compliance with procedures and insure quality of feed produced. These meetings usually are helpful in establishing and maintaining good morale and teamwork among employees.
Construct or modify the feed mill and adjacent buildings to minimize access to rodents, birds, insects and other pests, and locate them in an area that allows proper drainage.
Maintain the building and grounds as needed to assure a clean work place for employees and for the production of feeds. Litter, refuse, improperly stored equipment and supplies are hazards, remove them. Provide sufficient space for facilities and personnel to perform their job properly.
Examples of space needed for the production of medicated feeds include:
- Appropriate area for receiving and storing of ingredients and drugs
- Adequate space for grain processing, etc.
- Appropriate space for feed mixing
- Reserved area for equipment maintenance.
Equipment must meet safety standards and be installed properly. Test all scales and metering devices for accuracy upon installation and at least once per year thereafter.
Construct and maintain equipment to prevent lubricants and coolants from contaminating ingredients or feeds. Prevent excessive spills, leaks and dust problems.
Systematically monitor ingredients for quality factors throughout the entire process of purchasing, receiving, sampling and handling. Inspect all ingredients for any abnormality that may result in a quality risk when added to the feed, and take representative samples for assays. During this handling of ingredients, take care to prevent contamination.
Drugs and Premixes require special handling and record keeping. Records on drugs received must show the following information:
- Name of drug, including potency.
- Date received.
- Amount in pounds.
- Supplier’s name.
- Supplier’s code for drug (if applicable).
- Supplier’s lot or code number.
- Return of any damaged or unacceptable drugs.
Follow these procedures in the storage, handling and use of drugs:
- Check each drug for identification. Do not accept unless properly identified.
- Keep all drugs and premixes stored in a neat and orderly manner for easy identification. It is preferable to store drugs in a separate room.
- Code each bag or drug container with the supplier or company code for that drug.
- Store packaged drugs in the storage area in their original closed containers.
- Check bags for tears and any other abnormalities. Do not accept any drugs that are not in good condition.
- Properly identify, store, handle and control drugs in the mixing area to maintain their integrity and identity.
- Clean up any spilled drugs immediately, dispose of properly and record in the Drug Inventory Record.
- Use a separate scoop for handling each drug.
- Use drugs and premixes on a first received basis.
A daily inventory of drugs and premixes is required. Complete the drug inventory record at the end of each 24 hour period. Check usage of each drug against medicated feeds produced. Weigh the drug container before it is opened and account for every pound of drug in usage or adjustment. Examples of other adjustments include improper weighing, spillage, and out of condition. Cleaning, processing, and mixing of feed ingredients requires that personnel involved by thoroughly trained and properly supervised.
Considerations for proper GMP’s include the following:
- Screening of grains and use of magnets.
- Grind as uniformly as possible.
- Accomplish flaking of grain with proper amount of steam, temperature and roll tolerance.
- Standardize mixing directions for a feed mill. (Certain mixed feeds may require specific directions.)
- Prevent contamination.
- Check for accuracy for all scales used for weighing ingredients (including drugs) at least once per year as required by FDA.
Maintain FDA Complaint Files for Medicated Feeds for FDA inspection and include the following:
- Date of complaint
- Complainant’s name and address
- Name of feed
- Lot or control number or date of manufacture
- Specific details of the complaint
- All correspondence
- Description of investigation
- Disposition of complaint.
Quality Control Checklist for Feed
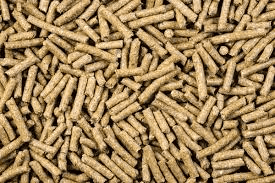
Following are three checklists that identify some of the areas needing attention by all involved in ensuring quality control in feed production
Checklist for Sources of High or Low Analytical Values
- Formulation error.
- Nutrient or drug instability.
- Moisture pickup or loss.
- Incorrect weights (batching errors).
- Dust losses.
- Non-uniformity of ingredient, supplement or premix insufficient mix time.
- Residues and cross contamination.
- Inadequate sampling methods Segregation in transit or of sample.
- Analytical errors.
Checklist for Overall System Efficiency
- Select intelligent and responsible suppliers.
- Select intelligent and responsible mill operators.
- Select adequate mixer.
- Adequate mixing times, Proper ingredient formulation.
- Use of appropriate feed binders.
- Limit conveying of premix and finished feeds.
- Accurate weighing equipment.
- Emphasize cleanliness and good housekeeping.
- Keep accurate records.
Checklist for Performance Evaluation
- Evaluate variation of incoming ingredients.
- Evaluate mixer efficiency.
- Evaluate efficiency of conveying feed from the mixer to the feed bunk.
- Evaluate variation of analytical procedures.
- Evaluate system efficiency.
Advantages of Quality Control in Feed Formulation
There are several advantages to submitting your raw materials and feeds to a quality control plan:
1. Legal: The manufactured feed must comply with the current legislation and the guarantees defined on the product label.
2. Zootechnical: The animal is certain to receive a feed that meets its nutritional constraints while allowing for the achievement of the targeted performance results.
3. Economic: The coherence between the quality of the raw material received in the feed mill and the nutritional values entered in the formulation software is validated.
4. Regular checks and updates of these values can result in a financial gain of several euros for each ton of manufactured feed.
5. Commercial: Customers satisfaction is sought by providing them with a feed that meets their expectations.
Read Also: The different types of fertilizers and how they work