Storerooms, warehouses, and distribution vehicles should be constructed to prevent access by rodents, insects, and birds, and carefully inspected regularly to ensure that preventative measures are effective.
There must be a high level of control over hygiene and storage conditions in warehouses and distribution vehicles similar to that given to processing operations.
When equipment is checked carefully, small problems can be identified and corrected before they cause downtime next season. Proper off-season checks will add value to farm equipment, increase its lifespan, and decrease operating costs.
Read Also: Popular Breeds of Ruminant Animals
General Considerations for Agricultural Warehouses
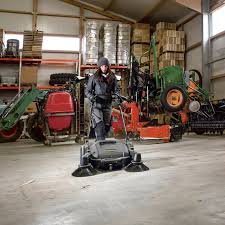
Modern warehouses are provided with material handling equipment, especially when bulk materials are stored. Leaking roofs and cracked walls must not be allowed in the warehouse. Bagged products are properly stacked on wooden platforms.
The effective spacing requirement for warehouse storage is 1.7m³ for one ton of grains. However, some allowances should be provided for stacks (platforms) and ventilation. Some warehouses are provided with aerators.
The floor of the warehouse must be well above the ground level to prevent flooding, and a solid foundation must be provided. Waterproof materials could be constituents of the foundation. This is to prevent water seepage. The floor should be provided with proper drainage.
Windows should be screened against insects, drainage channels and power cable ducting are fitted with devices to prevent entry by rodents, and the structure of the roof and walls is designed to prevent insects, rodents, and birds from gaining entry.
Doors are fitted with screens or air curtains and rooms are equipped with insect electrocution. Floors are covered with vinyl-based coatings to prevent cracks that could harbour insects and micro-organisms.
Common Causes of Food Spoilage in Storage
The main causes of spoilage of stored foods and ingredients are as follows:
1. Contamination by rodents, birds, insects, and micro-organisms
2. Contamination by dust or foreign bodies
3. Respiratory activity of fresh foods, or enzyme activity leading to the development of rancidity or browning
4. Losses from spillage, bursting of containers, etc.
5. Incorrect storage conditions such as exposure to sunlight, heat, and moisture.
Packaging and Material Handling in Agricultural Warehousing
Most foods are packaged for the protection and convenience of handling. Packages that are grouped into larger (or ‘unitised’) loads require less handling when they are moved through storage and distribution networks. Wooden pallets are commonly used to move unitised loads of cases or sacks by fork-lift or stacker trucks.
Read Also: The Ratio of a Male to Female Ruminants
Warehouse Procedures for Safe and Efficient Storage
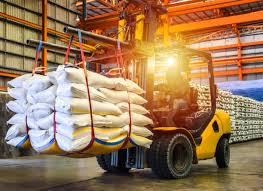
Working procedures in storerooms and warehouses ensure that sacks or cartons of food are stored on pallets or racks to keep them off the floor, with space to clean behind the stack.
They should be carefully stacked to the recommended height to prevent crushing or collapse and injury to operators. Lighting should be as bright as possible and at a high level to reduce shadowing caused by stacked pallets.
Use of Technology in Warehouse Management
Warehouse management systems are increasingly computer-controlled and are used to:
1. Monitor material movements into and out of the stores
2. Check stock levels and rotations
3. Check the use of materials in the process
4. Check the destinations for delivery of products.
Daily cleaning routines are used as part of a plan to prevent dust or spilt food from accumulating, which would encourage insects or rodents. Large warehouses use computerized truck-routing systems, which store information on stock levels, their location in a warehouse, and warehouse layout.
Computers that control automated guided vehicles (AGVs) have been used for several years. The AGVs follow fixed routes guided either by wires buried in the warehouse floor or coloured lines painted onto the floor.
These are now being replaced by ‘free-path AGVs’ in which the computer assigns an optimum route for each vehicle. Packaged goods are palletised and each pack and pallet is coded with a bar code that is read by a microprocessor.
The coded stock is allocated a storage location by the computer, which compiles both a map of the warehouse and current stock levels in its memory.
The progress of each AGV in retrieving or replacing stock is monitored and controlled using the information transmitted by an odometer in the vehicle and by bar-code directions that are displayed throughout the warehouse, which are read by a laser mounted on the truck.
Communal Storage Systems for Smallholder Farmers
Where farmers come together in informal groups, they often consider establishing communal stores that are managed by a trained store manager. The individual farmers can consolidate their stocks ready for the market by delivering to the communal store.
This arrangement may be the better option for smallholder farmers who do not have the capital to put up their own stores, have limitations of land available for the store, or do not know how to store commodities well for extended periods.
These stores work extremely well as bulking centres where large traders come and pick up truckloads of commodities (preferably of the same quality) at one time. The advantage to the big buyer is the reduction in the cost of buying through multiple aggregate traders with their multiplied handling costs.
Basic Factors in Agricultural Warehouse Design and Construction
Some of the basic factors to be taken into consideration in warehouse design and construction are as follows:
1. The site where the building is located must be well-drained and not subject to flooding. A swampy location will not only encourage the penetration of ground moisture into the stored produce but the soil bearing capacity would be reduced as the moisture content increases and there is a tendency towards failure.
2. The floor in addition should be made moisture-proof by incorporating a moisture barrier in the foundation layer before putting the final concrete.
3. The wall should be plastered smooth and devoid of any crack where insects may hibernate or hide.
4. The doors and windows should be tight-fitting to provide partially air-tight conditions for fumigation purposes which may be required from time to time. Such tight-fitting conditions will also help to control the entry of rodents.
5. The roof should be leak-proof to prevent the entry of rainwater into the store.
6. The eaves should be completely sealed such that they do not provide an avenue for entry by birds and rodents.
Space Requirement Considerations for Grain Warehouses
Usually, a warehouse is used to store grains in bags and stacked on pallets. The space requirement in a warehouse can be established using the following procedures:
1. Determine the number of bags using the relationship between the total amount of grains to be stored and the weight of one bag.
2. Decide on the number of bags per pallet, and this will give the total number of pallets.
3. Determine the dimension of a pallet which will depend on the dimension of the bag.
4. Decide on the arrangement of the pallets and the spacing between them, the spacing between the walls and those pallets nearest to the walls in both the length and width directions.
5. The height of the pile or stack will determine the height of the wall after making provision for headspace to aid ventilation.
Checklist for Off-Season Equipment Inspection and Storage
The following checklist is very important, as adhering to it will help to identify and solve problems of storage equipment:
1. Thoroughly clean all equipment with a high-pressure washer.
2. Lubricate all points.
3. Coat all parts that rust easily, such as ploughshares or chrome hydraulic cylinder rods, with a high-quality protectant.
4. Inspect all equipment for broken, bent, or worn parts. Repair or replace as necessary.
5. Apply touch-up paint to scratched or rusted areas.
6. Apply a generous coating of wax to help the equipment fight the effects of the elements.
7. Store equipment in a shed or under a tarp or heavy plastic if possible.
Do you have any questions, suggestions, or contributions? If so, please feel free to use the comment box below to share your thoughts. We also encourage you to kindly share this information with others who might benefit from it. Since we can’t reach everyone at once, we truly appreciate your help in spreading the word. Thank you so much for your support and for sharing!